We can be your reliable supplier!
Manufacturing process of denim material
The manufacturing process of denim is relatively unique. It is a product that is first dyed with indigo and sizing, and then woven. The production process of denim is also more complicated, mainly including the following steps
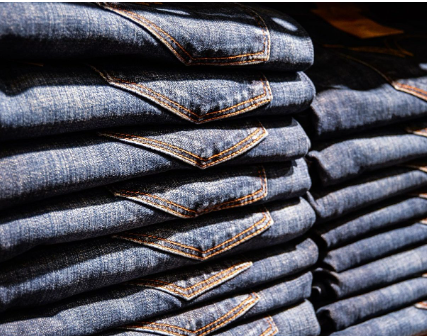
Dyeing and Sizing
There are three types of indigo dyeing of denim warp: rope dyeing, sheet dyeing and dangling dyeing. The first two are connected with sizing, and the latter is dyed and then sizing.
①Rope dyeing and sizing | On the ball warping machine, 350 to 400 warp yarns are arranged into multi-strand rope strips with a length of 10,000 to 15,000 meters, and then 12 to 36 strands of rope strips are fed side by side. Continuous dyeing machine, after dyeing, drying and winding into cans. On the long-chain shaft warping machine, the rope-like warp yarns are re-dispersed and wound into individual warp yarns. These warp yarns are then fed into a sizing machine for sizing and sizing as required The total number of warps is wound into a weaving shaft. The disadvantage of rope dyeing is that the dyeing, oxidation and washing are not very sufficient, and the equipment is huge, generally covering an area of about 1000m2 and a height of about 8m.
②Piece yarn dyeing and sizing: Piece yarn dyeing is commonly known as beam dyeing. It means that the warp yarns are warped into pieces instead of multi-strand ropes and sent to the dyeing machine. The characteristics of this dyeing are that the warp yarns are evenly arranged and the coloring is fast. It is uniform, fully oxidized, and easy to wash. After dyeing, the shade is pure, uniform and bright. In addition, the investment is low, and the area is about half of the rope dyeing machine. The disadvantage is that the cotton yarns are arranged in a single line, which is easy to produce tangles, especially under the liquid surface, it is not easy to be found. Due to the slow dyeing speed, two dyeing machines and one sizing machine can also be used for production, which can double the efficiency, that is, double warp beam yarn dyeing machine.
At present, the factories producing sheet dyeing machines include the sulzer company in Switzerland and the zell company in Germany.
③ Suspended ring dyeing: This method uses a dyeing tank, and the warp yarns are repeatedly dyed in this tank for many times until the depth requirement is reached. The technological process of dyeing and sizing is: alkali cooking (or wetting): sodium hydroxide 2~3g alkali-resistant penetrant 1g/L temperature 95~100 degrees time 20~30S Indigo dyeing: indigo (2+χ) g sodium hydroxide 2 . 5g hydrosulfite (85%) 2g/L bath volume is about 1000L temperature and room temperature time 20S Due to the low coloring rate of indigo on cotton fibers, and the poor fastness when dyeing at high temperature, the consumption of hydrosulfite is high and the shade is dark red , so use room temperature for multiple dyeing. This is the coloring feature of denim. The ventilation oxidation temperature is room temperature, 80 ~ 100S. In order to obtain pure color light, indigo dyeing does not use oxidizing agent and adopts ventilation natural oxidation. Because indigo is easy to reduce and difficult to reduce Due to the characteristics of oxidation, repeated oxidation is also used. The first temperature of water is room temperature. During the washing process, on the one hand, the floating color, residual alkali and impurities can be removed, and on the other hand, the oxidation can be continued to make it fully oxidized. In order to save the indigo dye, sulphur black can be used as the base instead of the alkali cooking process, and the indigo is first dyed into light gray and then overdyed. If the shade of the finished product is reddish after dyeing, the amount of sodium hydroxide can be reduced, and the amount of sodium hydroxide can be reduced if the shade is greener, which will not destroy the leuco state of indigo under normal circumstances.
Weaving
At present, shuttleless looms are widely used in the weaving of denim in the world, accounting for more than 80%. Among the shuttleless looms, the projectile loom is the most, followed by the rapier loom, and the least is the air-jet loom. The heavy denim processed by the projectile machine can reach 551g/㎡, and the one woven by the air-jet loom can only reach 407g/㎡.
Due to the different colors of warp and weft yarns in denim, yarn defects such as unevenness of weft yarns will be obviously exposed on the fabric surface. In addition, sometimes the original weft yarn is used, and the yellow and white yarn can also cause the weft stop. In order to prevent this phenomenon, a weft mixing device can be used, or the weft yarn can be dyed light gray. Weaving adopts large warp beam and large coiling. This is because the yarn count is thick, the turnover is large, and the machine cycle is fast, so a large warp beam must be used, generally the diameter is 800mm, and the winding shaft is usually 560mm. If the coil is separated from the body, the large package can reach 1500mm (about 600m of denim), but special vehicles and verification equipment are required.
Changes in weft tension during weaving can also produce fabric rungs. Although the single weft insertion on the shuttleless loom can avoid the tension difference between the shuttle and the shuttle of the shuttle loom, it is necessary to add a yarn storage device to eliminate the tension difference in the size of the package and the tension difference in the winding quality of the package. The yarn tension provided by the feeder to the gripper should be consistent, which is especially important for stretch fabrics.
The yarn count of denim is thick, the width is wide, and the warp tension is high. In order to clear the opening, the movement of the heald frame must be positive. Some shuttleless looms still use spring return healds, which are not suitable for thick and thick fabrics. Therefore, an external pedal device can be selected, and the pedal opening moves through the compound pedal, which can accurately control the movement of the heald frame. The movement of the pedals is transmitted through the rotor rod, the step rod and the heald frame drive link, and is equipped with a shed leveling device, which can adjust all the heald frames to the same height. Changes in warp tension during weaving can also cause weft defects (especially weft ends). This problem can be solved by using an external pedal device. Because when the weft yarn is broken to find the weft, the warp let-off, take-up and beating-up do not move. The pedals can move independently, and the warp tension will not change.
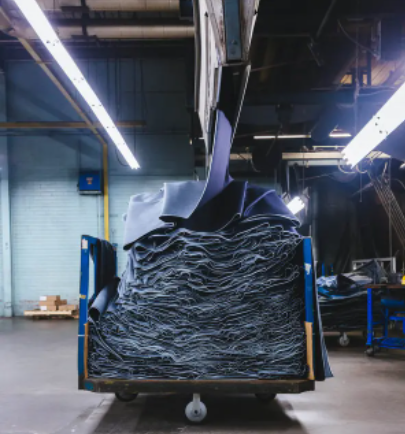
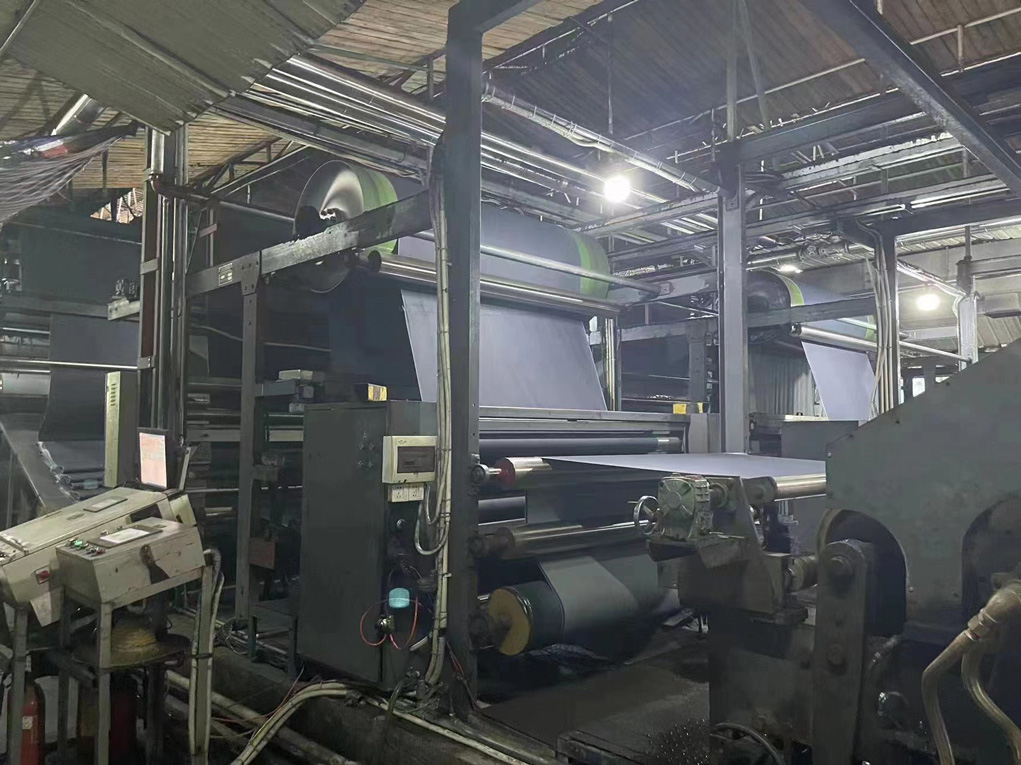
warping
1. The primary purpose is to make the tension, placement and winding of the yarn sheet or rope bundle uniform, and to wind a certain number of bobbins evenly and tightly on the warp beam or specially-made yarn with uniform tension and regular length. On the ball shaft, in preparation for the next dyeing and sizing process.
2. The first is the batch warping machine of type 1452A or GAI2I, which can meet the quality requirements for the combined dyeing and pulping production line.
Dyeing and finishing production process of denim
The manufacturing process of denim is relatively unique. It is a product that is first dyed with indigo and sizing, and then woven.
1. Dyeing and Sizing
There are three types of indigo dyeing of denim warp: rope dyeing, sheet dyeing and dangling dyeing. The first two are connected with sizing, and the latter is dyed and then sizing.
(1), rope dyeing
(Ring Yarn) Interspersed Winding – (Rotor Yarn) Warping – Rope Frame – Indigo Continuous Rope Dyeing – Long Chain Shaft Warp – Sizing – Weaving – Cloth Inspection – Post Treatment – Pre-shrinking
denim manufacturers
(2) Yarn dyeing and sizing
(Ring Yarn) Interspersed Winding-(Rotor Yarn) Warping-Indigo Dyeing Each Sizing-Weaving-Fabric Inspection-Singeing-Post-treatment-Pre-shrinking
(3) Suspended ring dyeing
This method uses a dyeing tank, and the warp yarn is dyed repeatedly in this tank until it reaches the depth required to stop. The process of dyeing and sizing is as follows:
The process of warp feeding-alkali cooking (or wetting)-water washing-indigo dyeing-ventilation oxidation (indigo dyeing)-ventilation oxidation is carried out six times-washing four times-drying-yarn storage-sizing-drying-winding